Más eficiencia en la gestión de los recursos y activos son los resultados de un piloto aplicado en Óxidos Encuentro y Planta Hidrometalúrgica.
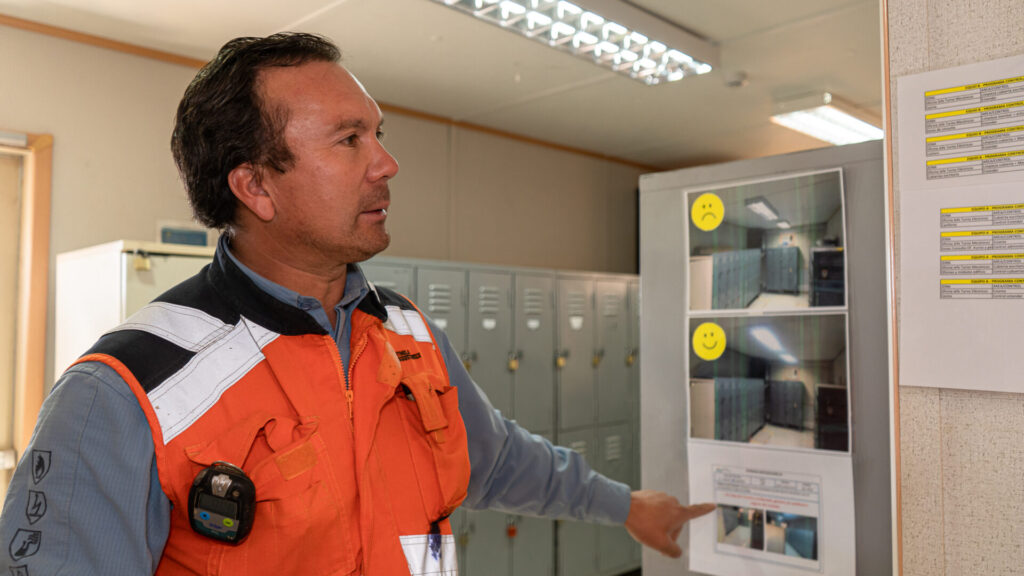
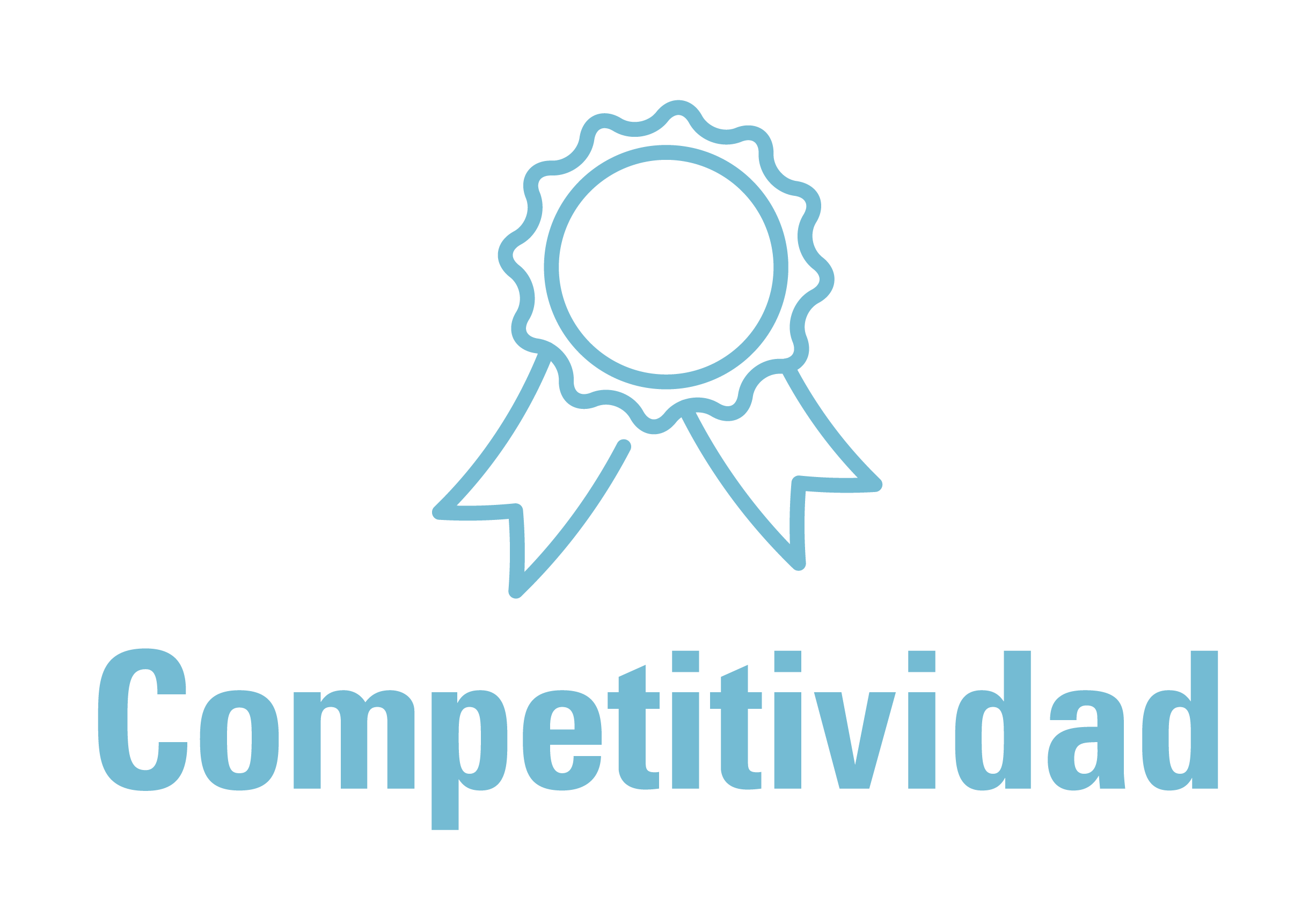
La transformación de una bodega en una sala de reuniones y la recuperación de insumos que no estaban catalogados, son algunos de los positivos resultados de la aplicación de un proyecto piloto basado en la metodología 5S en la gerencia de Mantenimiento Cátodos.
Esta técnica debe su nombre a cinco principios básicos que en español son Seleccionar, Ordenar, Limpiar, Estandarizar y Mantener. La metodología fue propuesta para aplicarla en el quehacer diario de los equipos de mantenimiento en Óxidos Encuentro (OXE) y la Planta Hidrometalúrgica.
“Comenzamos, aproximadamente, hace cuatro meses y llevamos un nivel de avance cercano a un 80%. Estamos en las últimas etapas del plan estipulado para este año y empezamos con los módulos de trabajo. Primero, a implementar un orden general del área y con eso logramos seleccionar ciertas cosas que eran necesarias y otras que no”, detalló el jefe de turno Mantenimiento Mecánico en la planta OXE, Jorge Duhalde.
La misma tarea se realizó en el taller eléctrico de la Planta Hidrometalúrgica, que logró un resultado no menor al utilizar esta metodología japonesa.
Rodrigo Hormazábal, ingeniero Sénior Eléctrico Instrumentación, cuenta que “uno de los de los puntos más importantes de este proceso fue adaptar una bodega que daba para todo y que actualmente la transformamos en una oficina de capacitación para nuestro equipo eléctrico, con una cafetería con estándar donde están bien definidos los puntos de la metodología 5S. Todo este trabajo lo han liderado los mismos jefes de turno y quiero destacar su compromiso porque así estamos avanzando en otras iniciativas de autoaprendizaje y recuperación de insumos que estábamos dando por perdidos”.
Compromiso transversal
El plan que impulsó la gerencia de Mantenimiento Cátodos todavía se encuentra en una etapa inicial, pero los resultados alcanzados revelan su efectividad y el compromiso de sus integrantes por adoptar la disciplina y mantenerla.
“Nosotros somos turno 7×7, turno contra turno, y es una implementación del área en general. Y como en todo orden de cosas, hubo un poco de resistencia al principio, pero al hacer partícipes a todos, incluyendo nuestras empresas colaboradoras, avanzamos y en definitiva es todo el edificio que está aplicando este cambio 5S”, comenta José Proboste, jefe de turno Mantenimiento Eléctrico e Instrumentación para la planta Óxidos Encuentro.
En tanto, el mantenedor eléctrico instrumentista del Área Hidrometalúrgica, Daniel Cisternas, agrega que “la experiencia ha sido bien agradable. Lo más difícil es el tema de mantener, ya que el turno es bien dinámico y a veces cuesta ser constantes con el orden, pero ha sido interesante y un desafío para el equipo poder apegarnos a esta metodología”.
0 comentarios